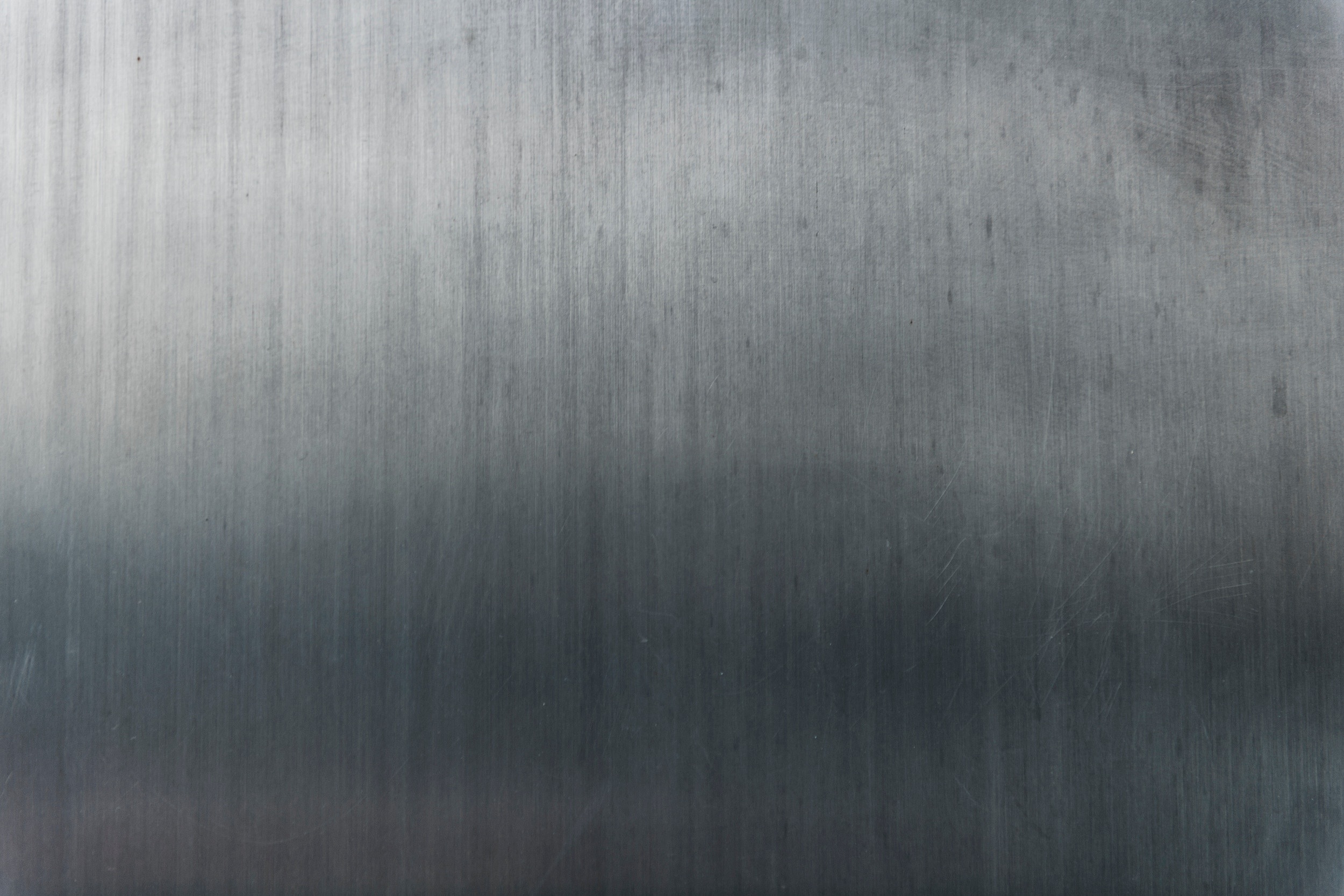
Development of Improved Industrial Alloys
Improving strength, heat resistance, weight, scrap rate of industrial alloys with the help of space measurments
In order to develop new innovative materials on Earth we must understand the full spectrum of phenomena influencing the complex process of microstructure formation during solidification. ESA’s materials solidification research carried out on the ISS and using sounding rockets is helping in the development of new knowledge-based casting methods for industrial aluminium alloys, which are being developed to reduce the occurrence of structural defects, thus helping to reduce the size of vehicle engines and improving efficiency as well as reliability. This research therefore not only has a positive economical influence within such industries, it also has a positive environmental influence with reduced fuel consumption and hence emissions. Numerical models that lie at the heart of these new methods rely on input parameters coming from ESA research. Parameters that cannot be accurately measured on Earth. Some thermophysical properties of high temperature metallic melts can be measured using the electromagnetic levitator, while solidification features and the dynamics of their formation can be obtained in both the electromagnetic levitator and the materials science laboratory, both of which are on the ISS. Sounding rockets tests complement these when it comes to more “difficult” alloys. These tests have been providing the fundamental information needed to accelerate the rate of innovation in manufacturing and materials engineering through computer simulations. The future use of X-ray radiography technologies on the ISS to observe the dynamics of microstructure formation in industrial alloys will even further extend the potential in this area of research as will experiments using the transparent alloys instrument. ESA has numerous industrial partners within this research (Innoval Tech., Arcelor-Mittal, Transvalor, InduSteel, AscoMetal, Aperam Alloys Imphy, Evraz, Alcoa Köfem Lt, Inotal, Nmeak, Hydro-Aluminium, Incaal, Schwemetall, Wieland, KME, DKI, Equispheres, RGS, VDM Metals, Areva, PX-Services, TATA Steel, Zollern, Netzsch, CSM). Modelling casting processes, and measuring properties of several industrially relevant alloys, will ‘bulk’ material features and related properties to be predicted. Snecma is also participating in a project aiming to understand and control how TiAl-based turbine blades can be reliably produced with superior properties in terms of strength and heat resistance, allowing significant reductions in fuel consumptions of future aircraft. The general belief is that a breakthrough is possible and that space measurements will have contributed importantly to that. Similar advantages are also expected for other segments, all leading to higher performance and process reliability (lower scrap rate), less energy consuming production and mobility. In addition to casting processes other potential applications include metallic glass production, 3D printing, spray forming and powder production.